First a little background, I started out with an 80gal saltwater tank back in the mid 80's. While it was mostly stocked with fish & invertebrates it also had some live rock with a few corals. I sold it shortly before heading for the west coast. Here is a pic shortly after I set it up:
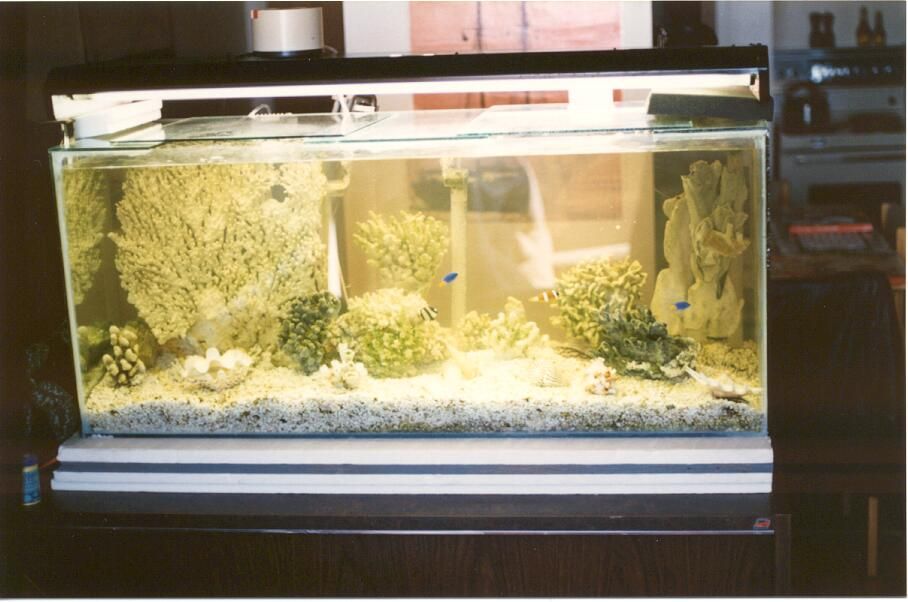